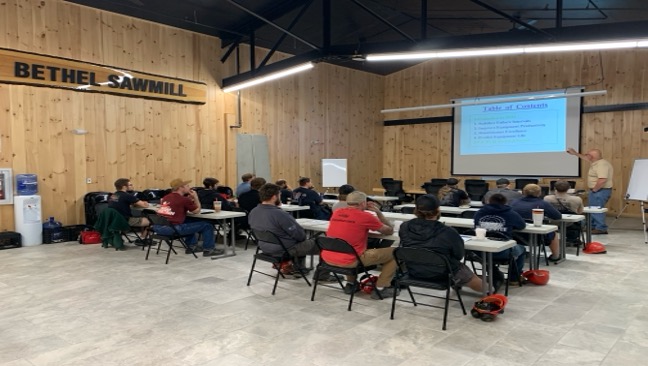
In the fall of 2024, our Bethel Eastern White Pine (EWP) Mill hosted a two-day Total Production Maintenance (TPM) training event with 17 Team Hancock members traveling from all three of our mills including Casco and Pittsfield. TPM training focuses on maximizing the productivity of equipment for its entire lifespan.
TPM fosters an environment where shared leadership shines and improvement efforts in safety, quality, cost, delivery and creativity are encouraged through all employee participation and feedback.
The concept for this training started back in 2016 when Mike Shane (Regional General Manager, EWP), Dan Wetmore (Casco EWP Mill General Manager), and Kevin Raven (Mill HR+ Safety Manager) attended a Lean Manufacturing Summit. There, they learned about TPM Training, how to bring that into their daily operations, and how to teach others about its principles. During this training, the group was struck by the phrase “imagine if there were no breakdowns, and there were no equipment stoppages?”. What if?
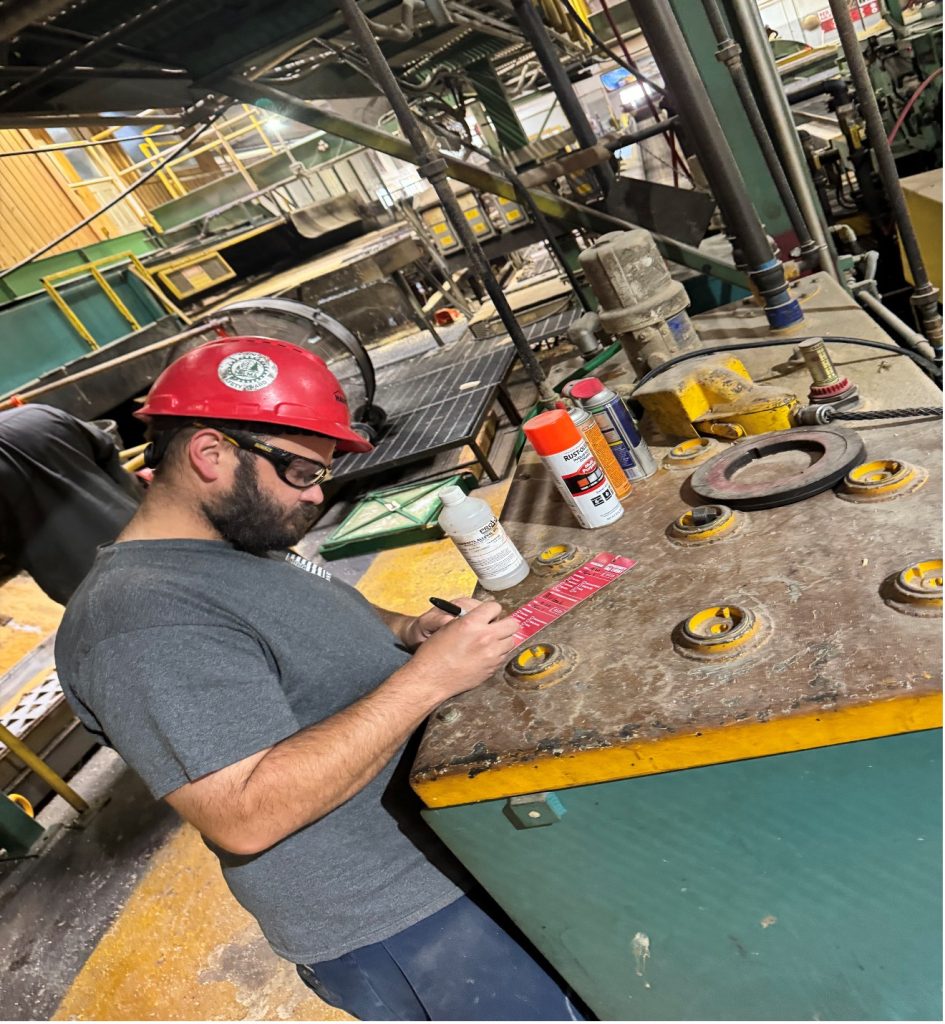
Fast-forward to 2024, and Hancock Lumber has hosted our 13th TPM training event with over 195 employees attending these trainings over the years.
In its current state, the training focuses on the four phases of TPM:
- Stabilize Failure Intervals
- Improve Equipment Productivity
- Maintenance Excellence
- Predict Equipment Life
The group focuses on giving attendees a good blend of classroom style learning and bringing their findings into the field for application during the two-day course.
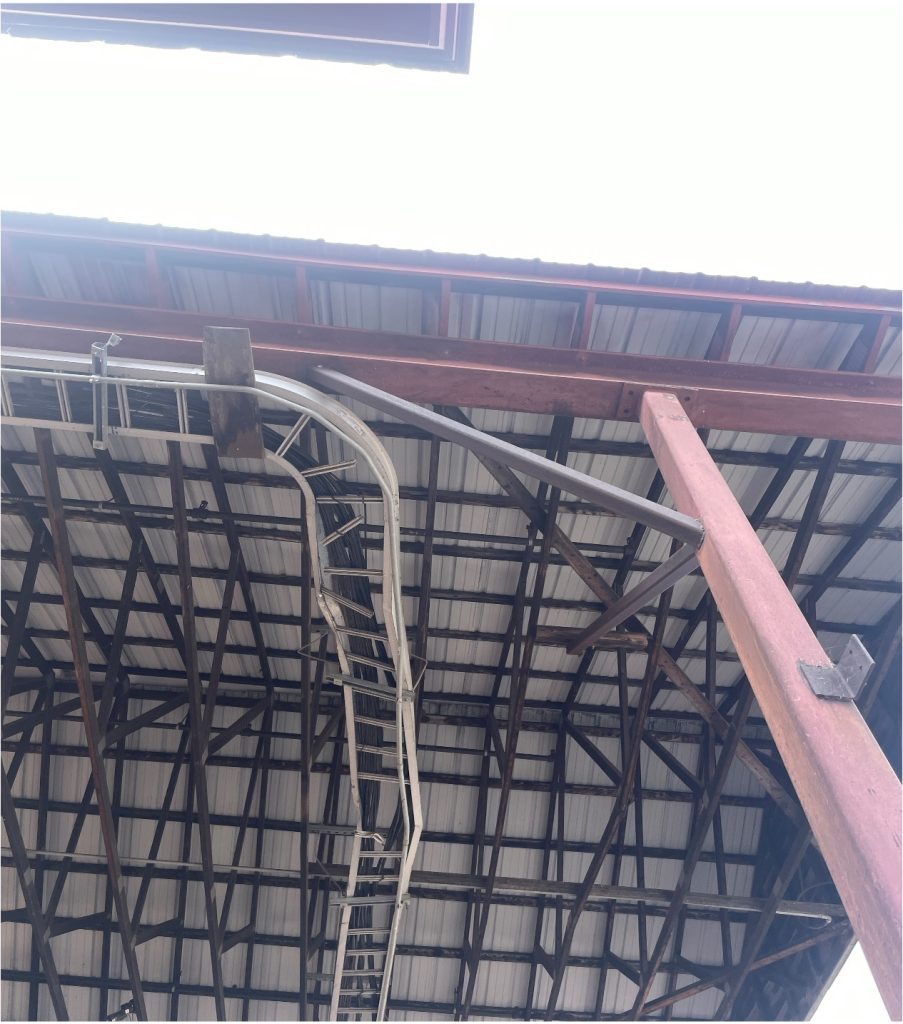
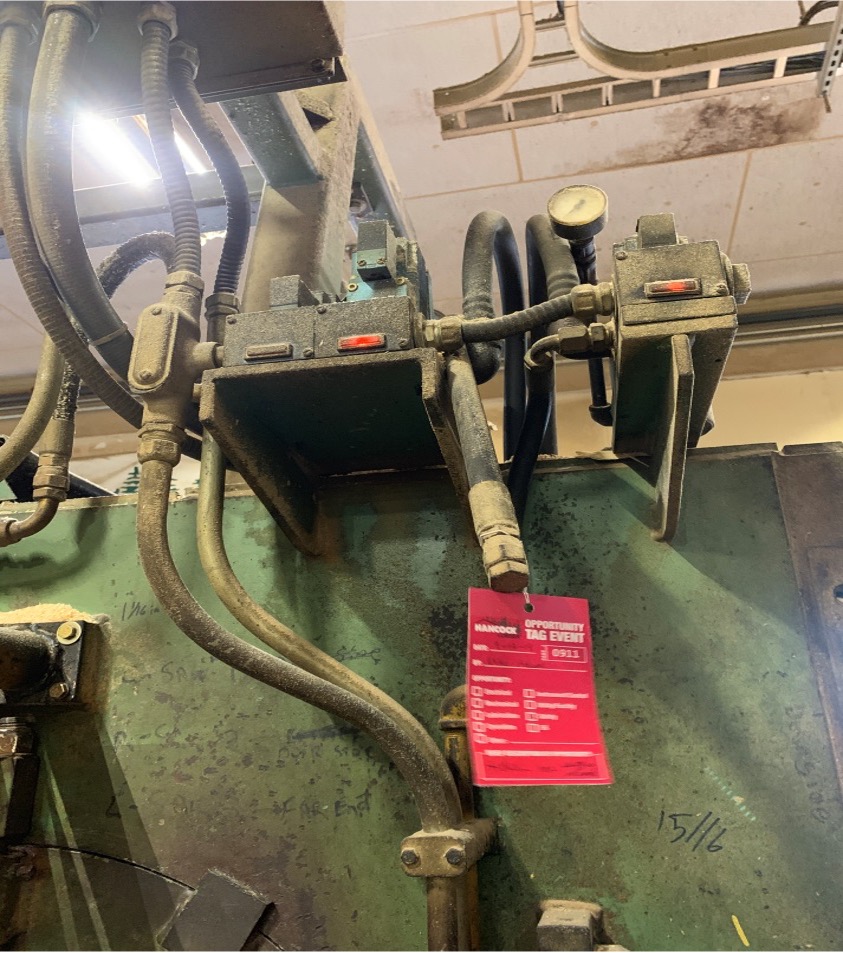
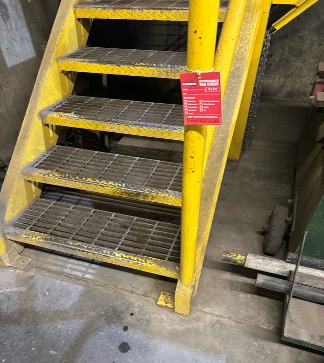
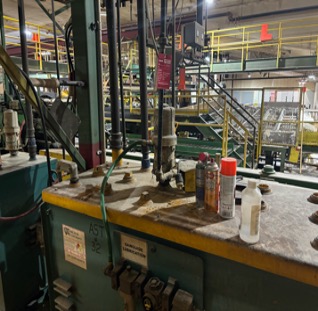
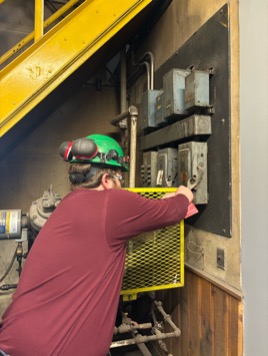
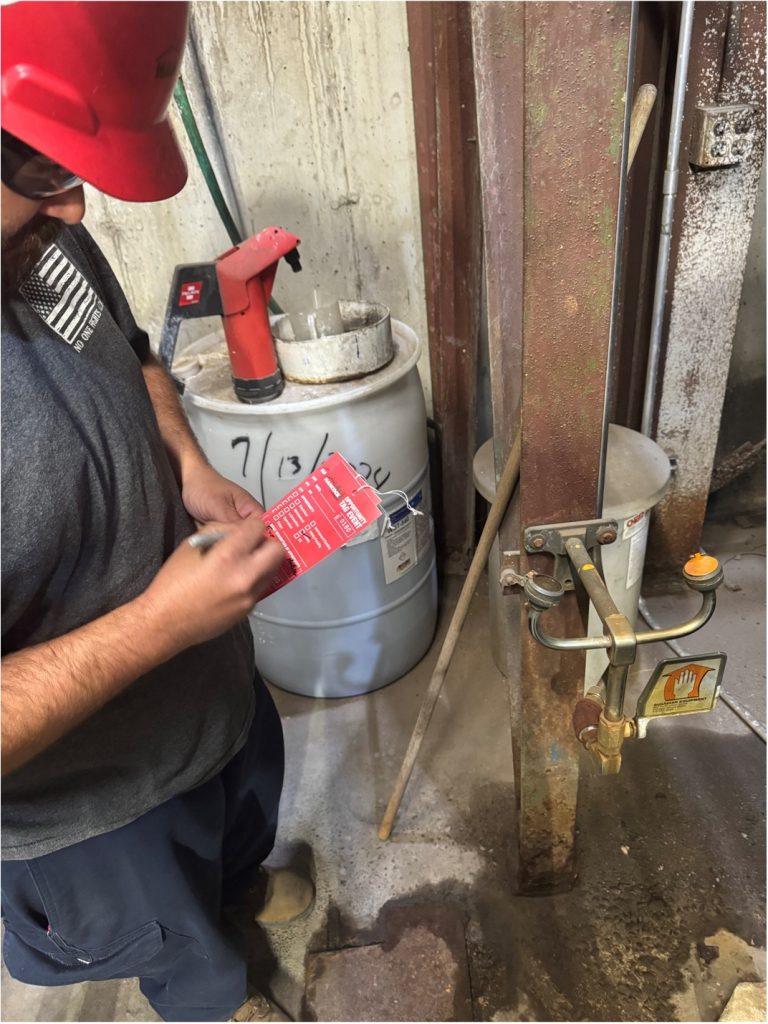
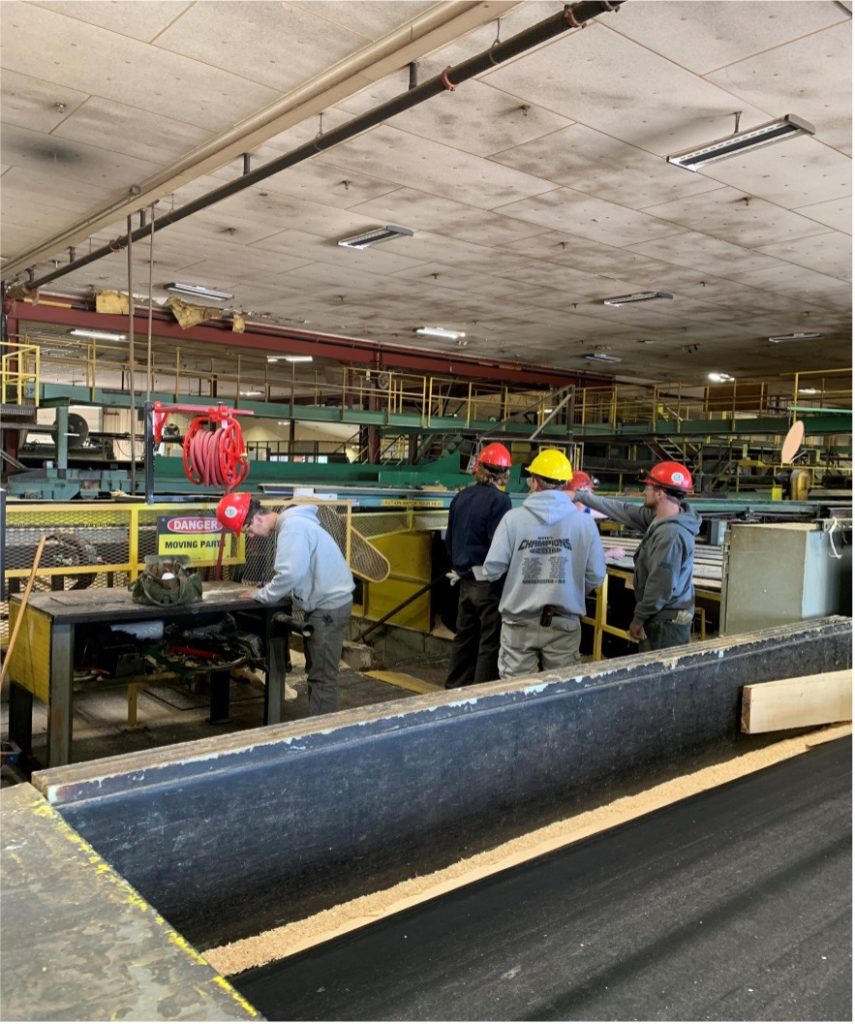

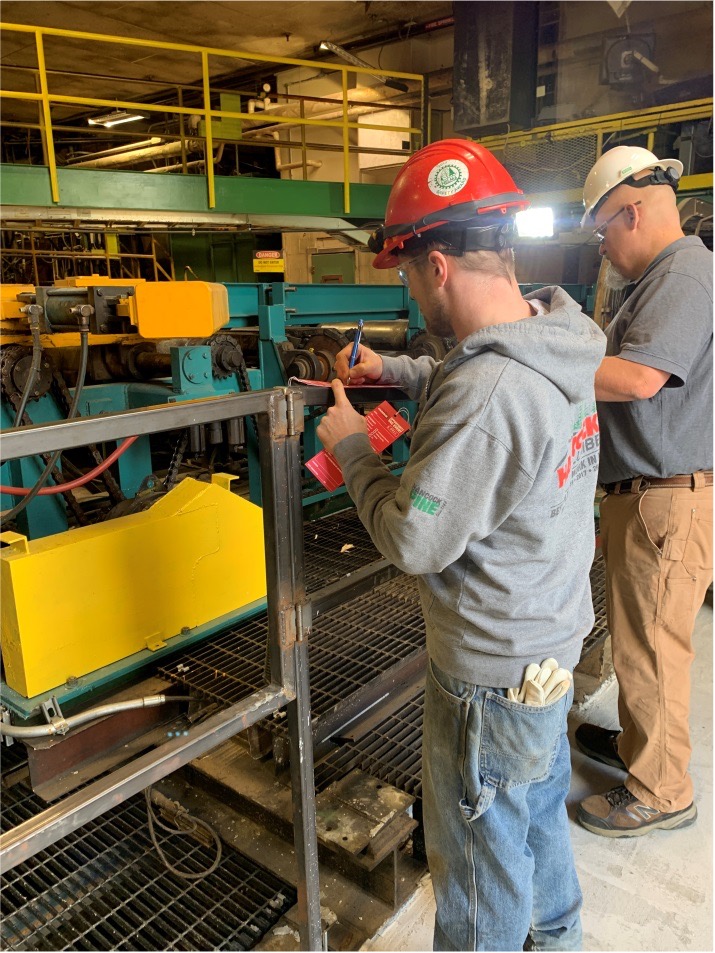
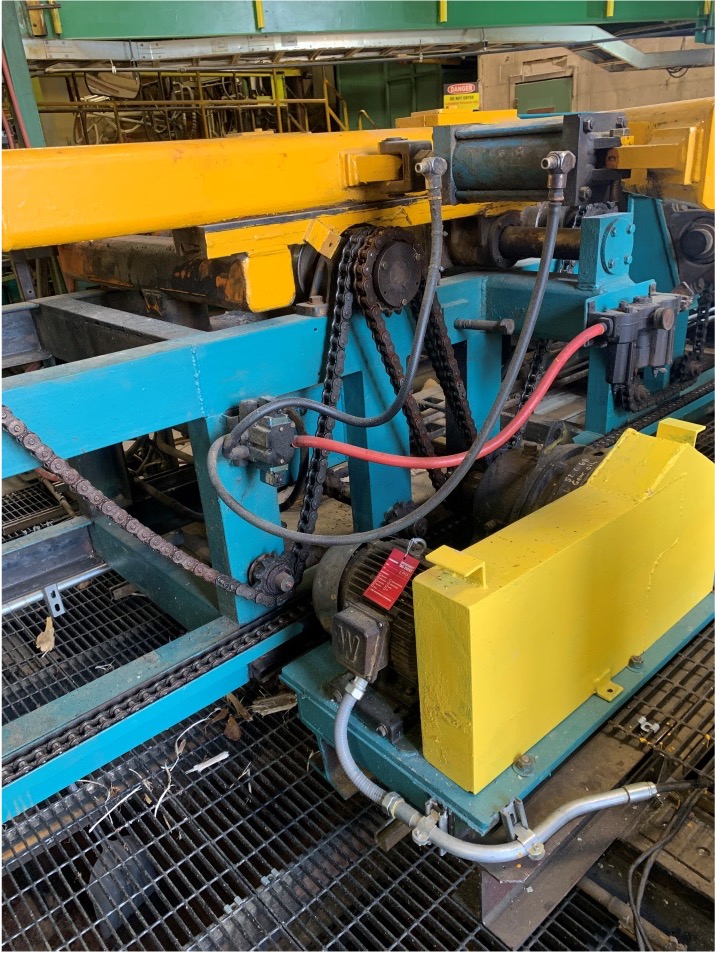
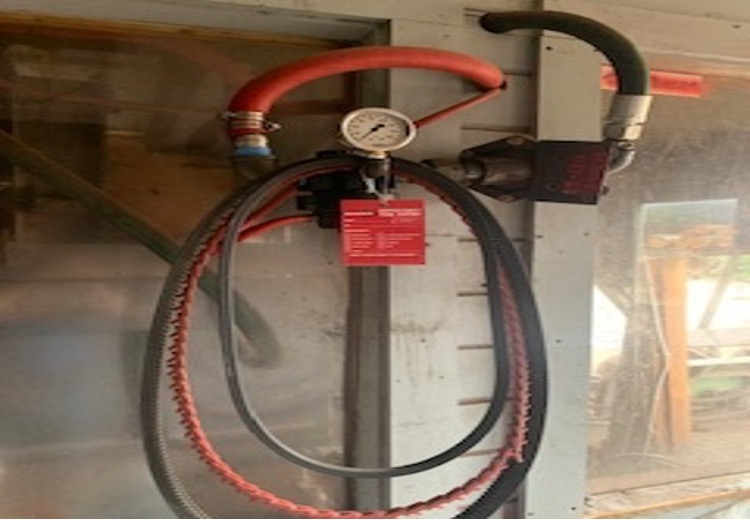
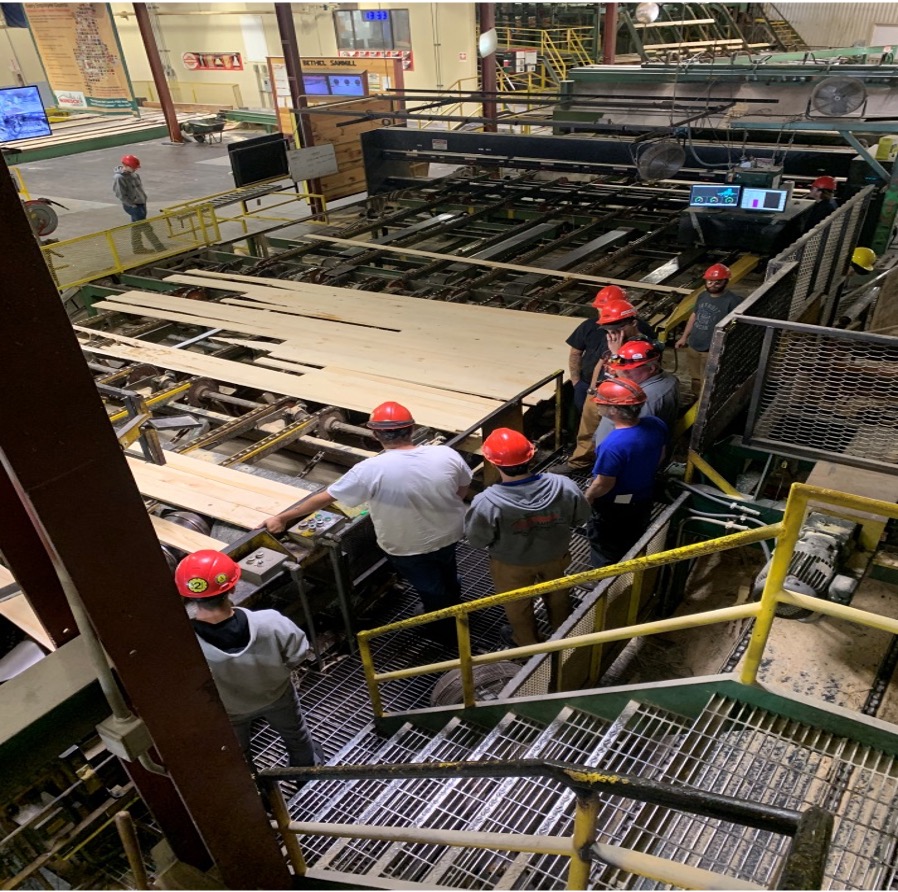
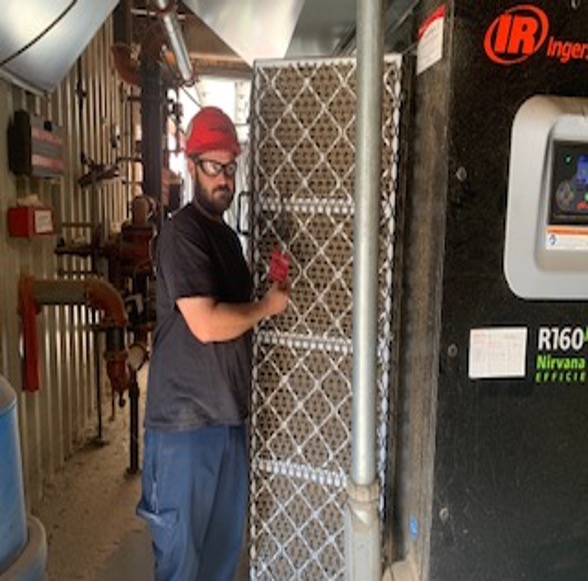
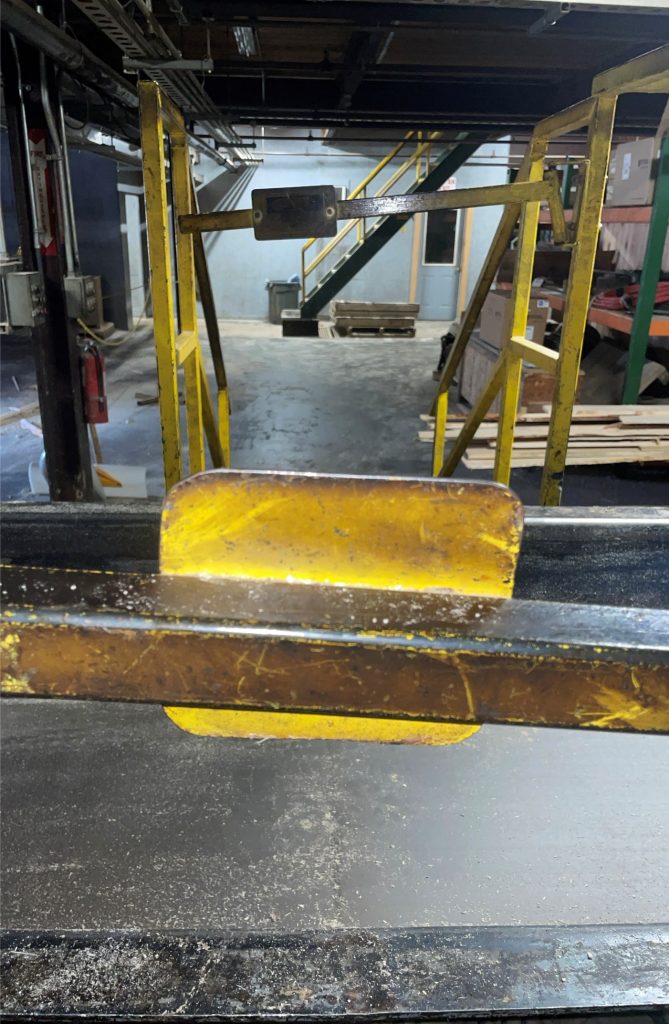
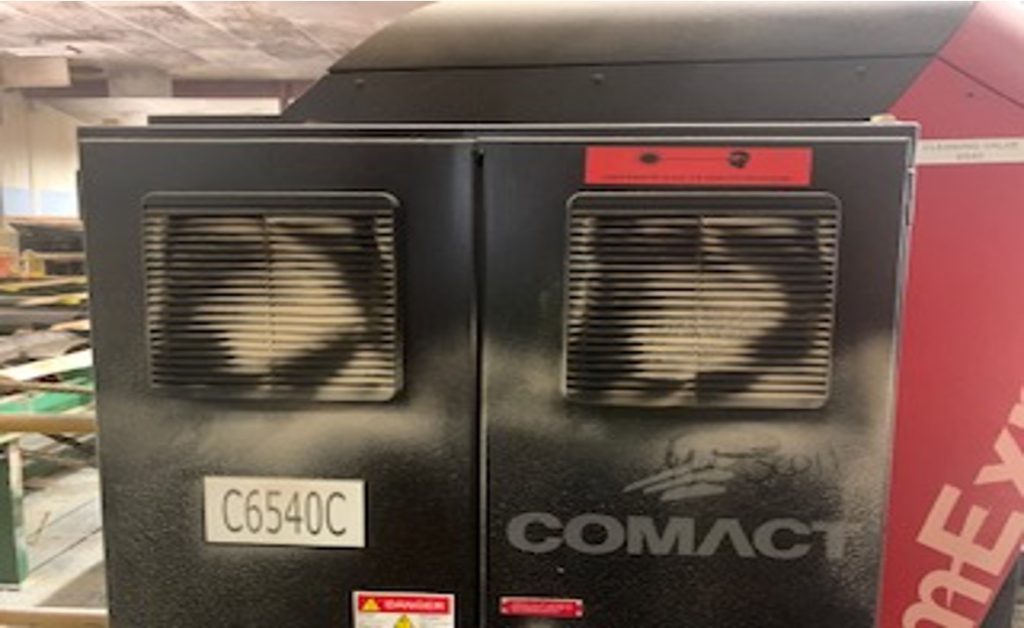

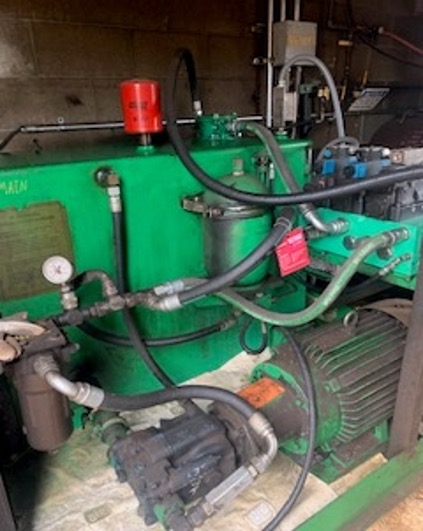
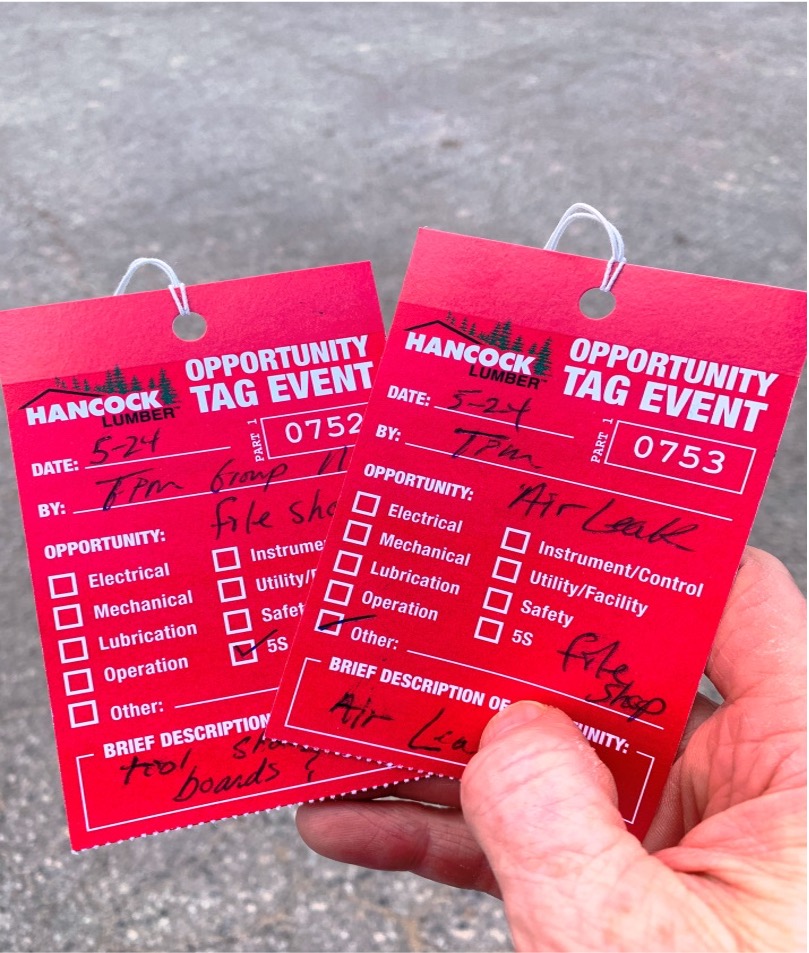
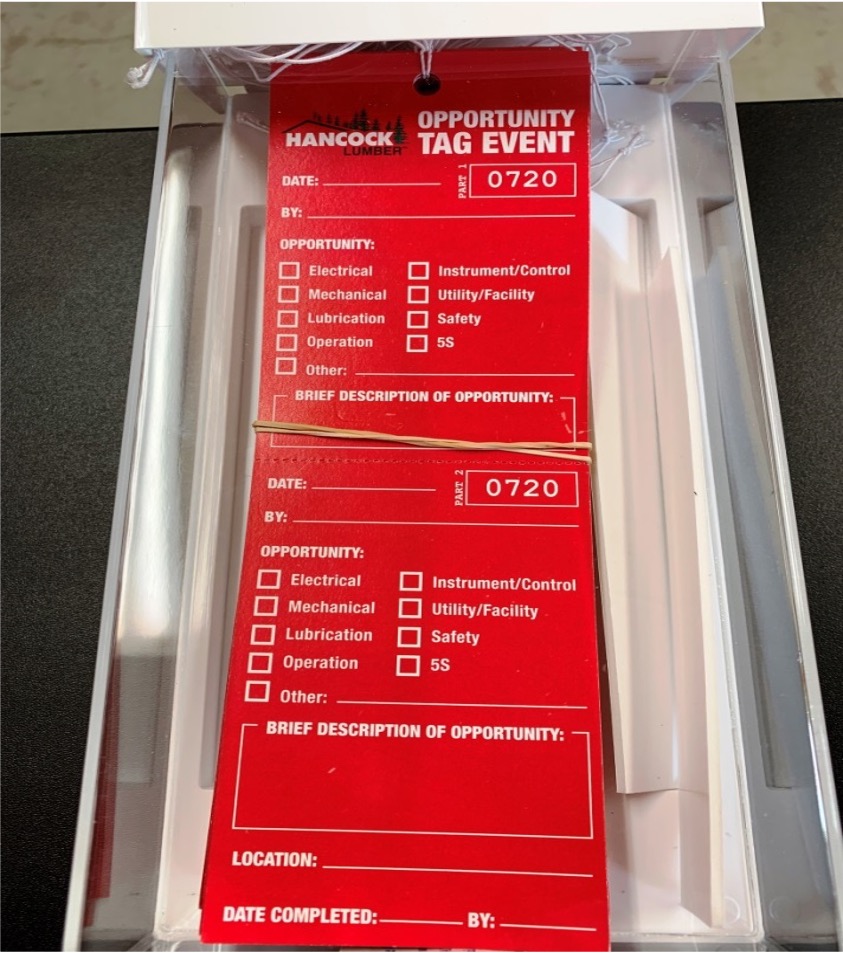
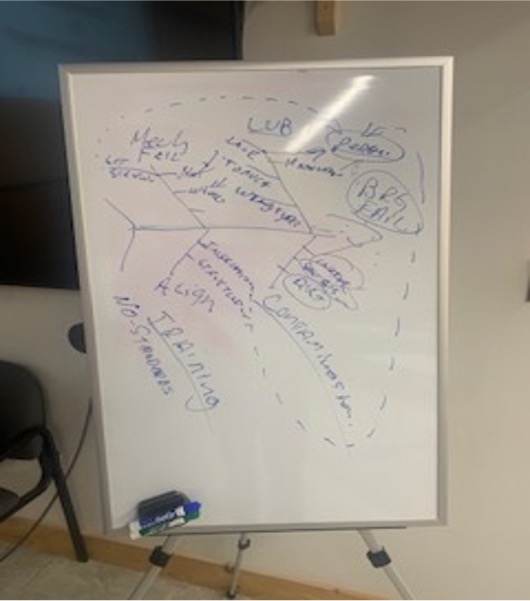
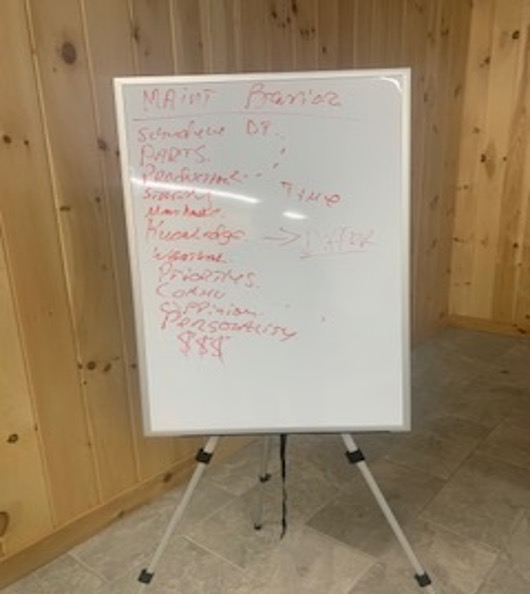
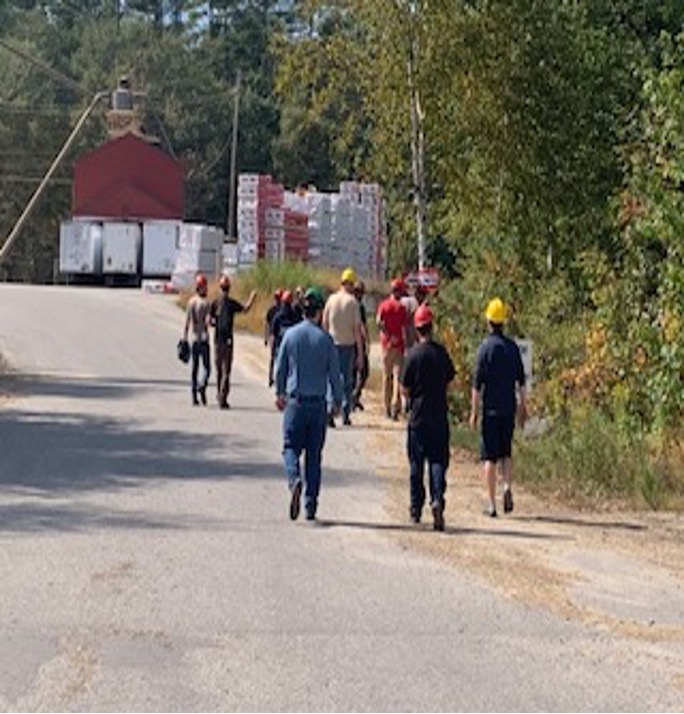
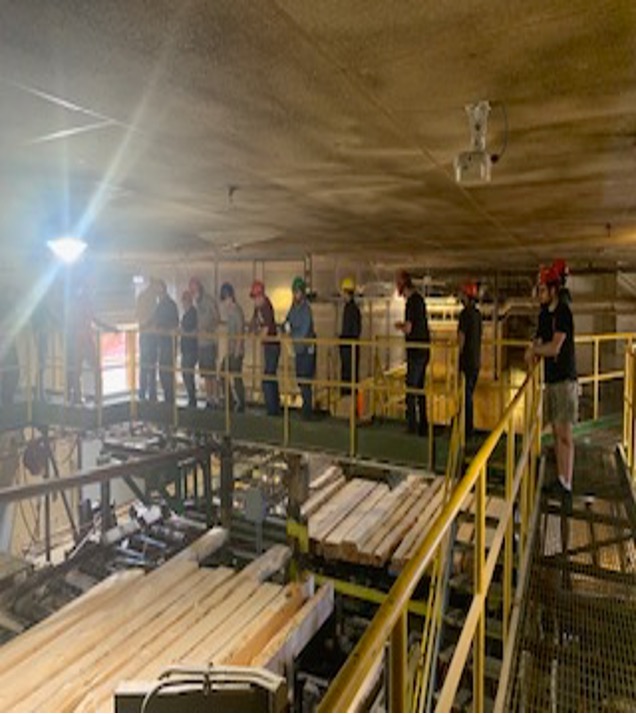
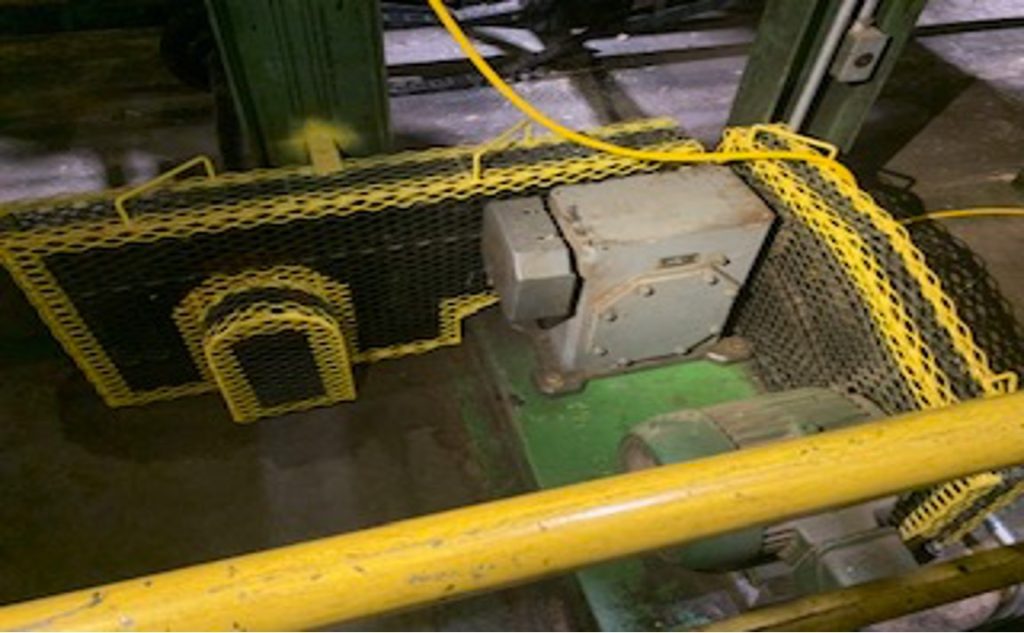
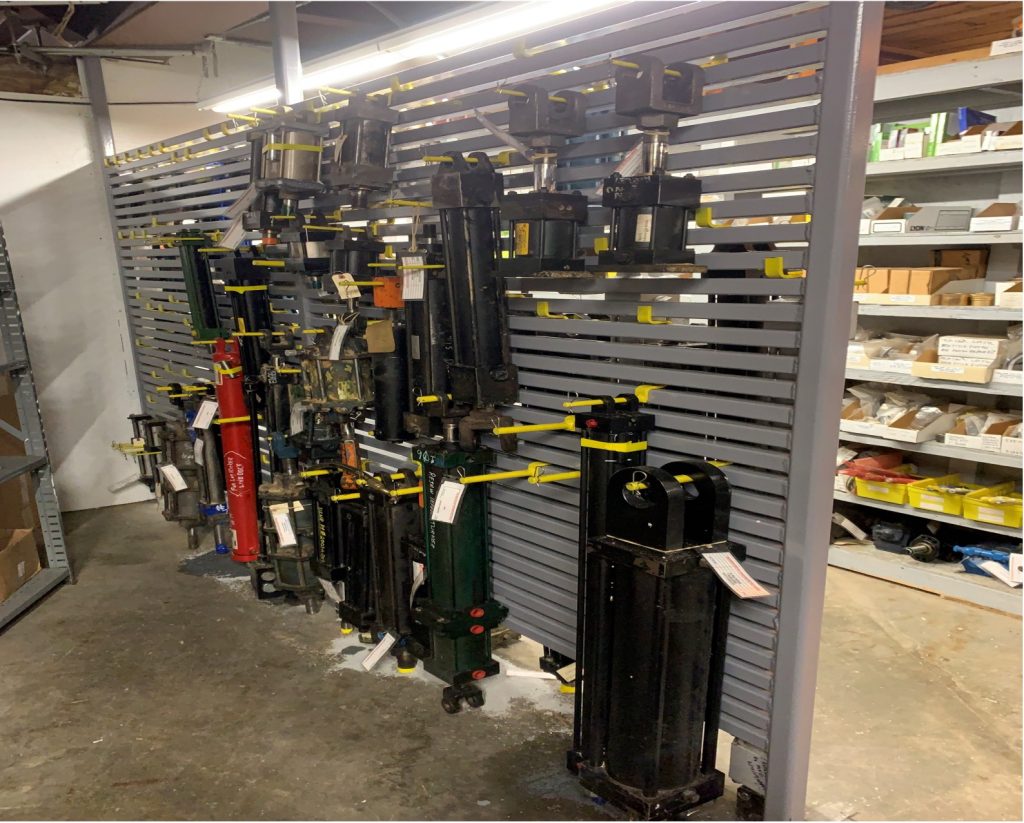