It started in 1848 with a hand-written contract for the construction of a mill. Ever since, Hancock Lumber has continued to invest in the future of eastern white pine manufacturing. With mills in the heart of eastern white pine territory, Hancock Lumber is one of the largest producers of the species in the country.
Reinvesting in the business has been foundational to Hancock Lumber’s success. Since 2023, the sawmill division has reinvested over $15 million dollars. Sourcing and funding new equipment is part one—having a vision, strategy, plan, and incredible team of people to execute is the other. Team Hancock evaluates new investments with diligence, focus, alignment and collaboration and executes successfully due to their talented and committed team’s planning and communication. From investments in people, safety, equipment, and culture, continuous improvement remains a top priority.
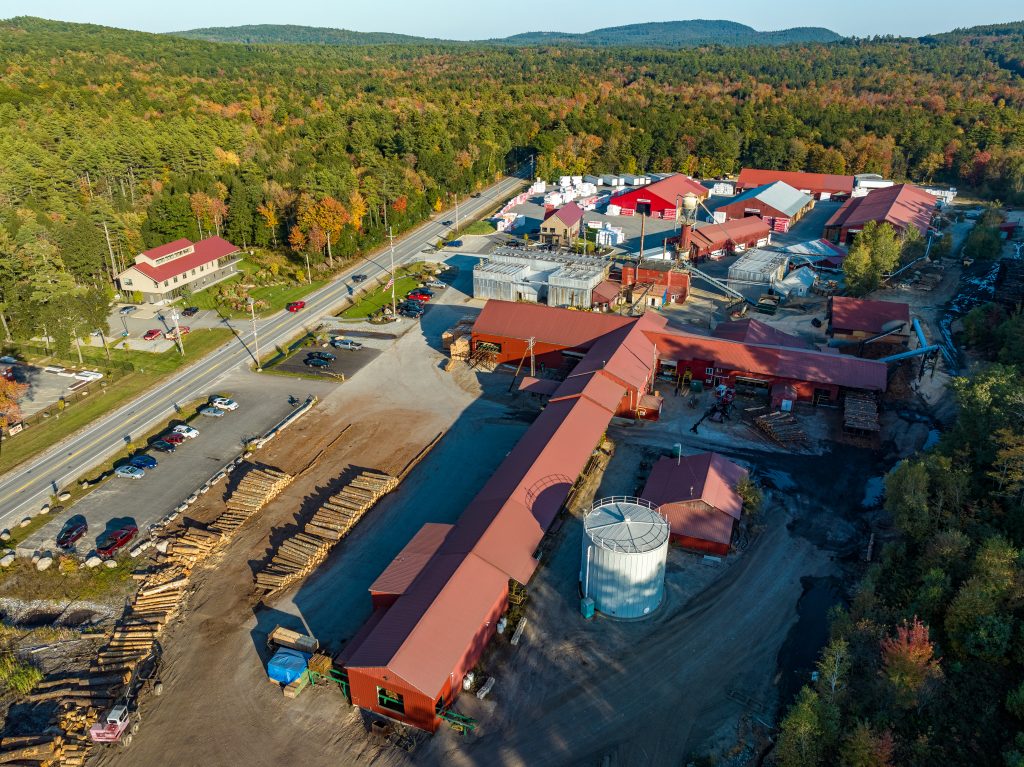
On the Casco Campus, the mill has integrated several new projects this year. In April the team went live with a new sash gang replacing a 50-year-old machine. While productivity and performance improve, the most important impact is on the people running the equipment and the how the human work experience is enhanced.
Kevin Hancock visited the site and Ben, the operator, shared that the new equipment literally changed his life, commenting that the job was much less stressful and that he was saving an hour of setup time daily. Kevin later shared in an email, “I finally got to the sawmill this morning to see the new sash running—it’s simply amazing! The change is dramatic. Great job to everyone involved!”
Sawmill Division COO, Aaron Schulte, recognized the monumental moment for two reasons—first, that a 1970’s piece of equipment lasted over fifty years, proving what a difference the team’s care and maintenance efforts had made. Aaron then recognized the team for their incredible planning that ensured a smooth install, giving a big shout out to Joel Leach who led the project so successfully!
Another noteworthy project in Casco is the continued investments and new products coming out of the Hancock ProFinish facility. From world-class priming to formulating stain colors to be applied to new end-match boards, reinvestments continue to enhance the employee AND the customer experience. Finally, the team also installed a new kiln this year, adding 15% more drying capacity.
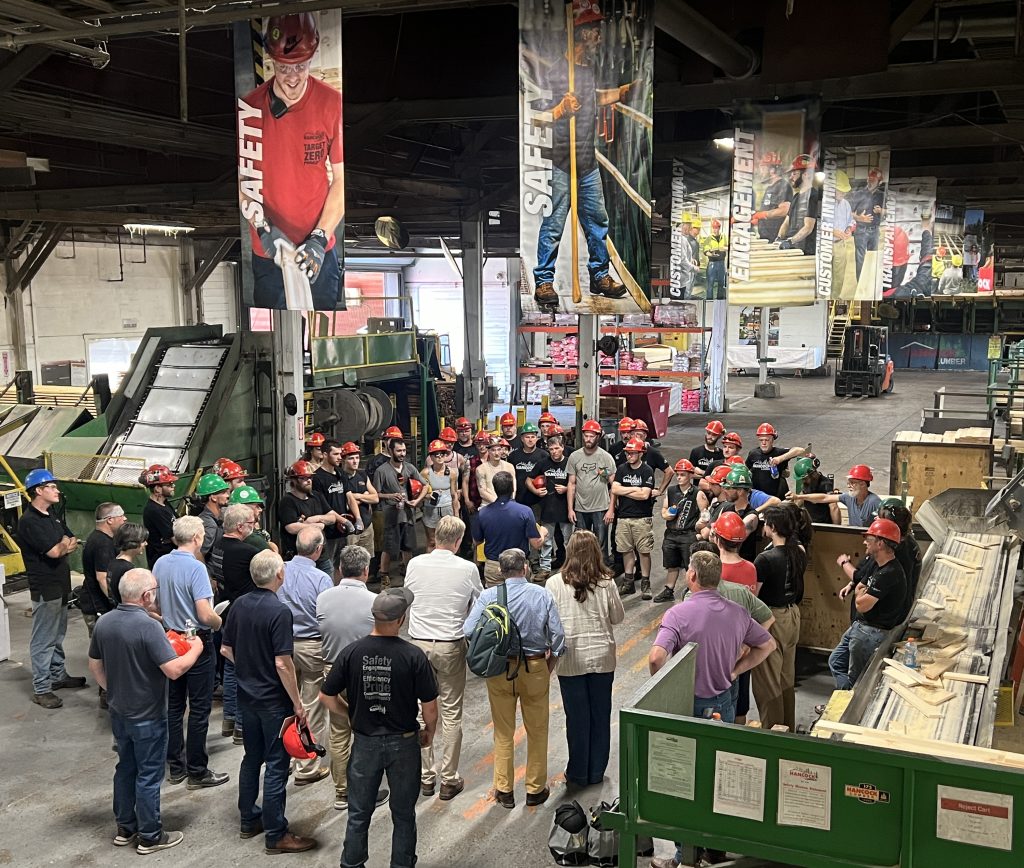
One hundred miles north, the Pittsfield team has also been modernizing equipment and technology. Team Hancock’s board of directors and executive team toured the mill this summer to see the capital projects first-hand and meet with the team.
Up next are plans to replace the existing vintage horizontal resaw with a modern Twin Horizontal McDonough system, improving a critical piece of equipment and increasing the mill’s capacity by up to 15%. Plus, the system will be fully integrated with automatic setworks, providing the ability to saw multiple thicknesses.
Another exciting Pittsfield project is swapping out the low-pressure boiler vessel with a Hurst HRT high-pressure vessel, along with installing a 275kW steam-driven micro-turbine. Continuing to reduce their carbon footprint, this new install will generate electricity from otherwise wasted energy from the biomass boilers that are used to dry lumber and heat the facility. Finally, Pittsfield also increased drying capacity with the installation of a new kiln.
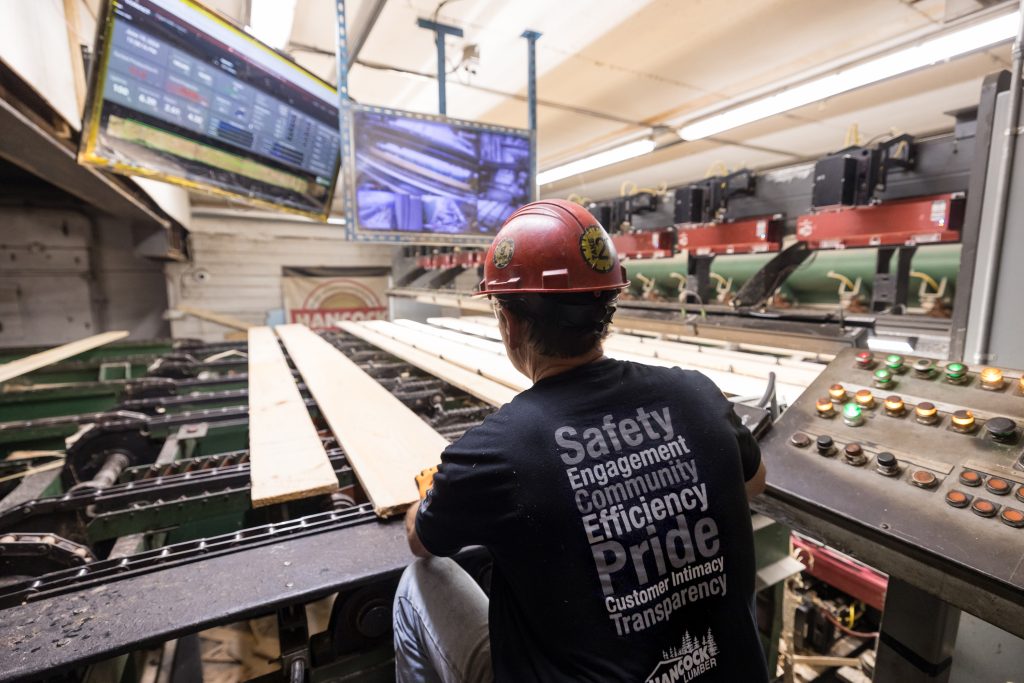
Team Hancock listens deeply to their team of 710 people and network of customers to determine top priorities and help inform capital projects. Shared leadership, dispersed power, and creating a workplace that enhances the lives of everyone who is a part of Team Hancock is foundational to their culture.